バーコードを活用した電子部品実装工場の改善提案事例
「職場改善前の課題」
電子部品実装工程では不良を作らないため実装機にセットする電子部品の品名、ロット番号を全て記入しなければなりません。これは誤組みと呼ばれる不良防止策のひとつで万が一不良が流出した場合でも履歴を調べることで「いつ」、「誰が」、「どの機種でどの部品を付けた」わかる仕組みです。
電子機器の内部に入っているプリント基板に実装(半田付け)する電子部品は機種によるが多いもので200種類以上の電子部品を使うこともあり、その電子部品の履歴(以下トレース)をとることでも非常に時間がかかってしまう。
実装機で自動実装している最中に部品が切れたときには部品交換記録用紙に部品セットリストに書かれている部品名を先ず記入し、今までついていた部品の品名と部品ロット番号を記入し、交換する新しい部品の品名とロット番号を記入し、最後に交換した人の名前と第3者確認の人の名前を記入するのがルールだった。
この部品交換する時間が1回で約3分はかかり、その間実装ラインは止まってしまう。
また不良が流出したときにその記録用紙を探す時間も多大で、古いものになると探すのに数時間を要することもあるのも問題。
これらの課題を解決するためにバーコードを活用した改善提案を行いました。
「職場改善の取り組み事項」
手書きのトレースを廃止し、バーコードシステムを導入する。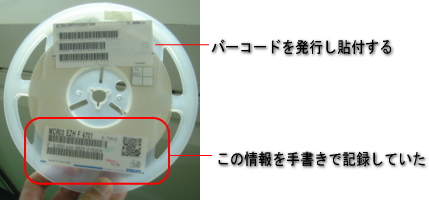
「改善に取り組む問題点」
1.バーコードシステムは非常に価格が高い2.バーコードを印刷する手間、貼る手間が増えるので作業者からの反対意見。
「改善取り組む問題の解決方法」
1.費用対効果が大きいことを経営陣に伝え説得した。2.増える作業と減る作業の差を説明し納得してもらった。
「改善前と改善後の比較」
改善前 | 改善後 |
受入工程は部品チェックのみ | 受入工程は部品チェックとバーコード発行貼付作業が増えた(部品1種/1分) |
外段取り工程 使用する全ての電子部品の出庫リストに部品ロット番号を記入し品名チェック(部品1種/40秒) |
部品チェックとロット番号記入は不要となった。 |
内段取り 部品リスト合わせて部品を機械にセットし、他の人が第3者確認を行う。 |
バーコードを読むとセットする場所を表示し、セットした場所を間違えるとエラーがでる仕組みなので第3者確認は不要。 (1段取り/5分) またハード的にセットミスは発生しない。 |
生産工程 部品が無くなり交換するたびに部品リストの品名を記入し、今までついていた部品の品名とロットb記入し、新しく交換する部品の品名とロットb記入し、第3者確認もしていた。 部品が切れる毎に3分はラインが止まっていた。 |
部品が切れると品名バーコードとロット番号バーコードとリールIDバーコードを読ませて部品をセットするだけ。(15秒) |
生産終了後 部品リストに合わせてセットしていた部品をチェックする。部品1種につき5秒 |
チェックの必要なし。 |
スポンサードリンク |
「職場改善の効果」 バーコードシステム導入にかかった費用 ・150万円(ソフト、ハード込み) ・バーコードプリンター 5万円 ・データ保存用PC(余っているPCを使う) 合計155万程度 ランニングコスト バーコードラベル1枚5円 生産時間の変化 1日4段取り、1機種40部品(平均)、月22日稼動で計算 |
改善前 | 改善後 |
受入工程 部品チェック/1部品15秒 4段取り分で160部品 所要時間40分 |
部品チェックとバーコード発行貼付作業(部品1種/1分) 160部品*1分15秒 所要時間200分 |
外段取り工程 使用する全ての電子部品の出庫リストに部品ロット番号を記入し品名チェック 160種*40秒 所要時間107分 |
部品チェックとロット番号記入は不要となった。 所要時間0 |
内段取り 部品リスト合わせて部品を機械にセットし、他の人が第3者確認を行う。 40種*1部品セット30秒+第三者確認5分 所要時間25分 |
1部品セット20秒*40種 所要時間13.3分 |
生産工程 平均部品交換数5回*4機種=20回 1部品交換時間3分 所要時間60分 |
所要時間 15秒*20回 所要時間5分 生産工程は機械ラインのため1分当たりの賃率は高い |
生産終了後 最終部品チェック 部品1種/5秒*160部品 所要時間13.3分 |
チェックの必要なし。 所要時間0 |
改善前の合計時間 245.3分 (通常賃率工程185.3、機械工程60分) 1日あたりの金額 (通常工程1分40円、機械工程120円) 通常賃率工程 185.3*40円=7412円 機械工程 60分*120円=7200円 合計14,612円 |
改善後の合計時間 218.3分 (通常賃率工程213.3分、機械工程13.3分) 1日あたりの金額 (通常工程1分40円、機械工程120円) 通常工程 213.3*40円=8532円 機械工程 13.3分*120円=1596円 合計10,128円 |
一日当たりで4,484円の改善効果があり、月(22日)では89,680円、年での効果1,076,160円となります。
イニシャルコストで150万以上かかったとしても1年半で回収できる非常に画期的な改善事例です。
今回のこの改善事例では単に効率アップだけでなく、不良のポテンシャルを下げ、顧客の信頼度もあがり、万一不良が発生してもデータ化されているため、すぐに該当ロットが特定できるメリットもあります。
改善提案前はバーコード貼付の煩わしさなど後ろ向きだった作業者も作業時間短縮で楽になったとのコメントもあり成功した改善提案事例です。
スポンサーリンク
バーコードでの職場改善事例関連ページ
- 節電対策で現場改善
- 職場の改善事例.comは実際に行ってみた改善提案事例をご紹介する業務改善専門サイト。
- 工具の整理整頓・定置化管理で改善
- 職場の改善事例.comは実際に行ってみた改善提案事例をご紹介する業務改善専門サイト。